Transforming Industries: The Role of a Die Casting Mold Factory
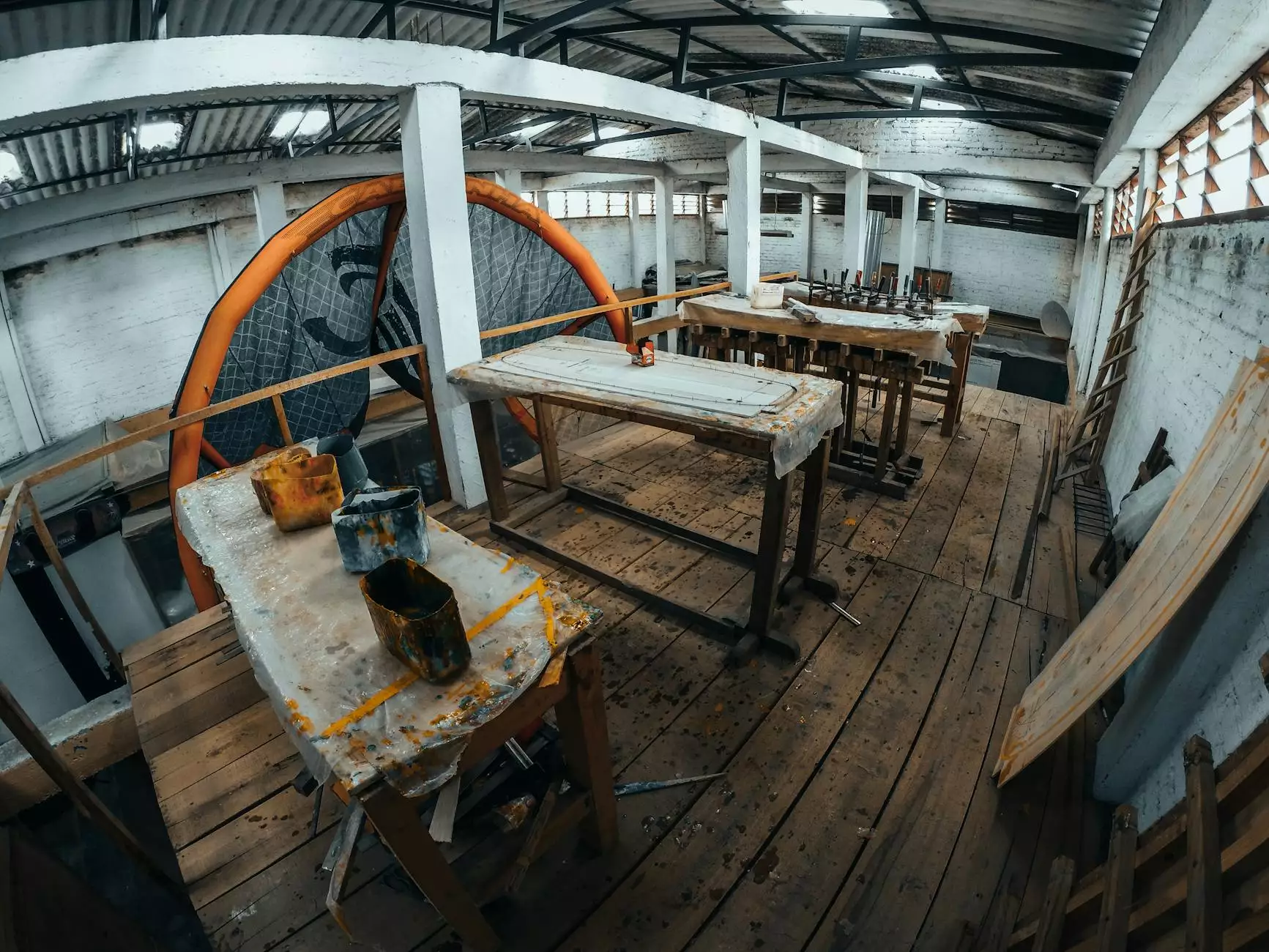
In today's fast-paced manufacturing environment, the demand for precision and efficiency has never been higher. At the heart of many production processes, particularly in industries such as automotive, aerospace, and consumer goods, lies the die casting mold factory. This article delves deep into the vital functions, innovations, and future trends of die casting, highlighting its importance in the realm of metal fabricators.
Understanding Die Casting
Die casting is a manufacturing process that involves forcing molten metal into a mold cavity under high pressure. This method not only ensures high precision and minimal waste but also allows for complex shapes that would be impossible to achieve through traditional manufacturing methods. The types of metals commonly used in die casting include:
- Aluminum
- Zinc
- Magnesium
- Copper
The Significance of a Die Casting Mold Factory
Within the framework of manufacturing, the role of a die casting mold factory is multifaceted. These factories serve as the backbone of metal fabrication, facilitating the production of high-quality components that are essential in various industries. Here's why they are crucial:
1. Precision Engineering
One of the primary advantages of die casting is the precision it offers. Components produced in a die casting mold factory are known for their tight tolerances, ensuring that each part fits perfectly into its designated application.
2. Efficiency in Production
Die casting is often more efficient than traditional methods, as it allows for the rapid production of parts. This efficiency translates into lower costs and faster turnaround times, which is invaluable in sectors where time is critical.
3. Material Efficiency
Die casting minimizes waste, as the process uses only the amount of metal needed to create each part. This not only conserves resources but also reduces costs, making it an environmentally friendly option for manufacturers.
Innovations in Die Casting
As technology evolves, so too does the die casting industry. Innovative techniques and advancements are continually being integrated into the operations of a die casting mold factory. Key areas of innovation include:
1. Advanced Materials
The emergence of new materials, including lightweight alloys, has expanded the possibilities for die casting. These materials can enhance performance while reducing weight, particularly beneficial in the automotive and aerospace sectors.
2. Automation and Robotics
Automation has revolutionized die casting operations, with robots streamlining processes from metal handling to quality inspection. This technology enhances consistency, safety, and speed, setting new benchmarks in manufacturing efficiency.
3. 3D Printing in Molding
Utilizing 3D printing technology for mold creation has allowed die casting mold factories to reduce lead times significantly. 3D-printed molds can be developed quickly and economically, providing manufacturers with the flexibility to adapt to changing market needs.
Quality Control in Die Casting
Quality control is paramount in a die casting mold factory. Several measures are implemented to ensure that every produced part meets industry standards:
- Dimensional Inspection: Utilizing advanced measurement tools to verify that parts meet required specifications.
- Material Testing: Conducting tests to ensure the integrity of the materials used, including tensile strength and hardness evaluations.
- Finish and Surface Quality Checks: Inspecting for surface defects or imperfections, ensuring the final products are visually appealing and functionally sound.
Applications of Die Casting
The applications of components produced in a die casting mold factory are vast and varied. Here are some of the key sectors that benefit from die casting:
1. Automotive Industry
The automotive industry relies heavily on die cast components for parts such as engine blocks, transmission cases, and structural supports. The precision and durability of these parts contribute significantly to vehicle performance and safety.
2. Electronics
In electronics manufacturing, die casting is utilized for creating housings and components that are both lightweight and heat-resistant, critical attributes for electronic devices.
3. Industrial Machinery
Many industrial machines utilize die cast components for their durability and strength. These parts endure significant stresses and are crucial for the efficiency of machinery operations.
Sustainability and the Future of Die Casting
As industries worldwide contend with the pressures of sustainability and environmental responsibility, die casting is evolving. A die casting mold factory can adopt more sustainable practices by focusing on:
- Recycled Materials: Increasing the use of recycled metals in production processes.
- Energy Efficiency: Implementing energy-saving technologies in operations to reduce carbon footprints.
- Waste Reduction: Developing processes that minimize scrap and waste, further enhancing efficiency.
Choosing the Right Die Casting Mold Factory
When selecting a die casting mold factory, it is essential to consider several factors to ensure high-quality production and reliability:
1. Experience and Expertise
Look for a factory with extensive experience in die casting and a strong understanding of various industry needs. This expertise often translates to superior quality and problem-solving capabilities.
2. Capabilities and Facilities
Evaluate the factory's capabilities, including their types of machinery, technology, and the range of materials they can work with. This will determine their ability to meet specific production requirements.
3. Commitment to Quality
Choose a factory that prioritizes quality assurance through rigorous testing and adherence to industry standards. This commitment will help ensure consistent, high-quality production.
Conclusion
In conclusion, a die casting mold factory plays a critical role in modern manufacturing, offering precision, efficiency, and sustainability. With continual advancements and innovations, the industry is poised for growth, further solidifying its importance across countless sectors. As metal fabricators, these factories not only enhance production capabilities but also contribute significantly to the economy and technological progress. By understanding and supporting die casting production, businesses can ensure they remain at the forefront of their respective industries.