The Transformative Role of Injected Molded Plastic in Business
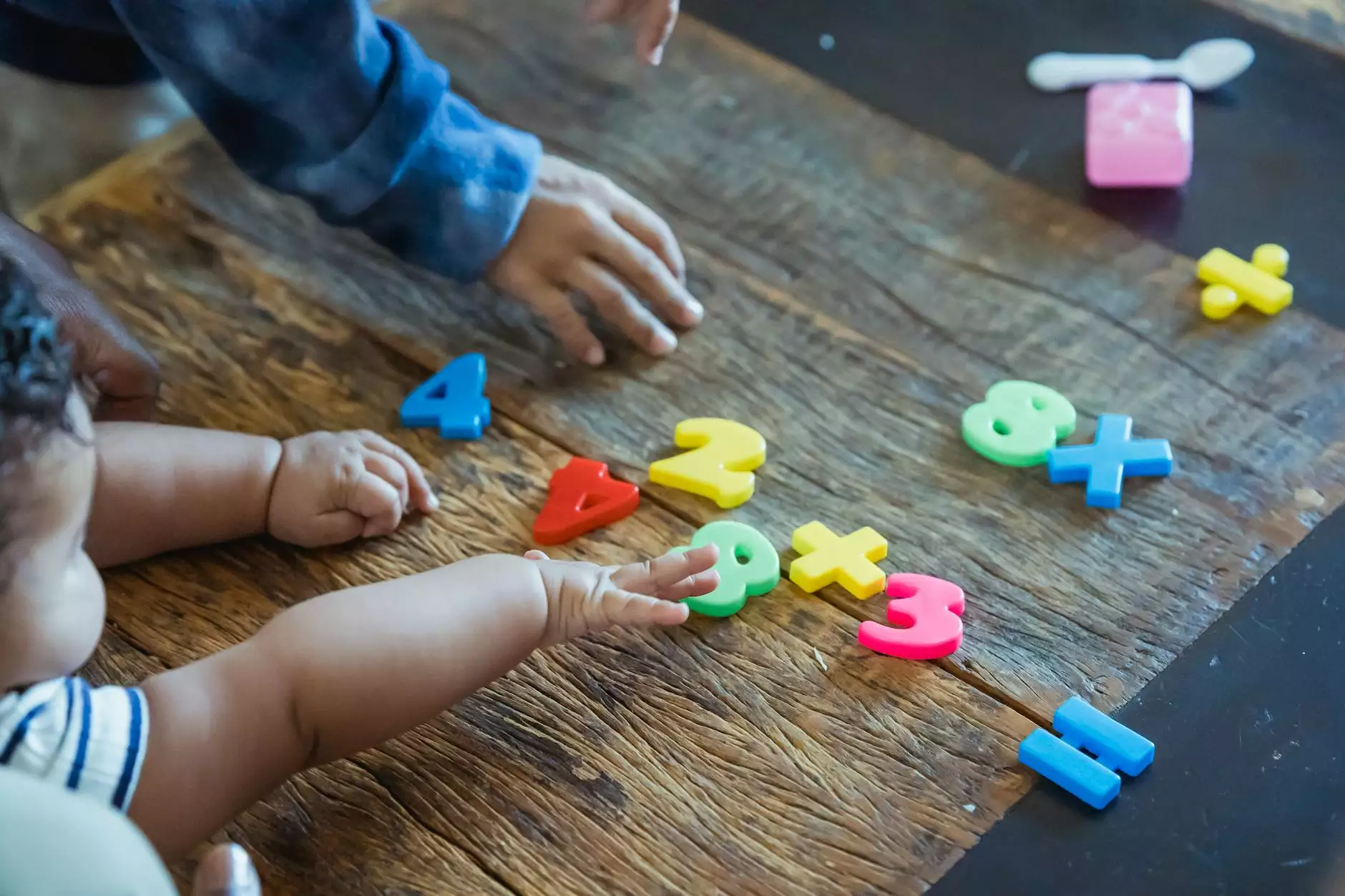
Injected molded plastic has become a cornerstone in the modern manufacturing landscape, especially in industries such as electronics and medical supplies. This advanced technology not only streamlines production but also enhances product quality, making it indispensable for businesses aiming to maintain a competitive edge.
Understanding Injected Molded Plastic
At its core, injected molded plastic involves the process of melting plastic pellets and injecting them into molds to create intricate shapes and designs. This technique allows for a high degree of precision and efficiency, making it a popular choice for manufacturers across various sectors.
The Advantages of Injected Molded Plastic
Businesses in the electronics and medical industries can significantly benefit from the use of injected molded plastic. Here’s why:
- Cost-Effectiveness: The efficiency of the injection molding process lowers production costs while enabling mass production of complex parts in short timeframes.
- Design Flexibility: Manufacturers can create intricate designs that would be difficult or impossible to achieve with traditional manufacturing methods.
- High Precision: Injection molding ensures that every part produced is identical, which is critical for electronics and medical supplies where precision is paramount.
- Durability: Injected molded plastic components exhibit excellent durability, resisting impacts and wear, which is vital for products used in demanding environments.
- Environmental Efficiency: Modern injection molding techniques often use recycled materials, minimizing waste and reducing the carbon footprint.
Exploring the Applications in Electronics
The electronics industry has been revolutionized by injected molded plastic, leading to the production of high-quality products with enhanced features. Here are a few key applications:
1. Electronic Housings
Injected molded plastic is extensively used to manufacture housings for various electronic devices, including smartphones, computers, and household appliances. The ability to create lightweight yet robust housings helps in improving the overall efficiency and aesthetic of electronic products.
2. Connectors and Switches
Many connectors and switches used in electronics are produced using injected molded plastic. They benefit from the precise dimensions achieved through molding, ensuring reliable connectivity and user experience.
3. Casings for Consumer Electronics
From wearable tech to home entertainment systems, injected molded plastic plays a crucial role in producing casings that not only protect the inner components but also provide an attractive finish.
The Impact of Injected Molded Plastic on Medical Supplies
In the medical field, where safety and reliability are non-negotiable, injected molded plastic has proven its worth. The following exemplify its impact:
1. Medical Device Components
Critical devices such as syringes, inhalers, and diagnostic equipment rely on injected molded plastic components for reliable performance. The precision in manufacturing ensures that these components function as intended, thereby safeguarding patient health.
2. Protective Equipment
As the demand for personal protective equipment (PPE) surged, injected molded plastic facilitated the rapid production of masks, face shields, and other crucial items, ensuring availability in times of need.
3. Sterilizable Products
Injected molded plastic can be engineered to withstand sterilization processes, making it suitable for single-use medical products that meet stringent hygiene standards.
Quality Control and Compliance
In both the electronics and medical industries, adherence to quality standards is critical. Injection molding companies, such as Nolato, prioritize quality control through:
- Advanced Monitoring: Employing sophisticated equipment to monitor the injection process and ensure each part meets the required specifications.
- Regular Testing: Conducting rigorous testing procedures to validate the performance and safety of molded components.
- Compliance with Standards: Ensuring all products comply with local and international regulations relevant to electronics and medical equipment.
The Future of Injected Molded Plastic
The future of injected molded plastic looks promising, with ongoing advancements in technology and materials. This evolution is fueled by the increasing demand for sustainable manufacturing practices and enhanced product performance. Innovations such as:
- 3D Printing Integration: Combining injection molding with 3D printing techniques to produce hybrid components.
- Smart Plastics: Integrating sensors into plastic products to enable smart functionalities.
- Bio-based Materials: Developing eco-friendly alternatives to traditional plastics to meet growing environmental concerns.
Why Choose Injected Molded Plastic for Your Business?
For businesses in the electronics and medical supply sectors, investing in injected molded plastic can yield significant advantages:
- Scalability: Easily scale production to meet fluctuating demands without compromising quality.
- Customization: Tailor components to fit specific needs and improve product differentiation in the marketplace.
- Enhanced Lifecycle: Products are designed for longevity, minimizing the need for replacements and fostering customer trust.
- Rapid Prototyping: Accelerate the design process, enabling businesses to bring products to market faster.
Conclusion
In conclusion, the adoption of injected molded plastic is transforming how businesses in the electronics and medical supply industries operate. The benefits ranging from cost efficiencies to enhanced precision and durability position this manufacturing process as a cornerstone of modern production strategies. Companies like Nolato exemplify the successful integration of advanced injection molding techniques, ensuring that businesses can meet the growing demand for high-quality products tailored to the needs of their customers.
As we look to the future, the continual innovation in injected molded plastic holds boundless potential for driving growth and efficiency across various industries. Embracing this technology will be pivotal for any business aiming to achieve sustainable success in today's competitive landscape.