CNC Precision Parts Manufacturers: Driving Innovation in Metal Fabrication
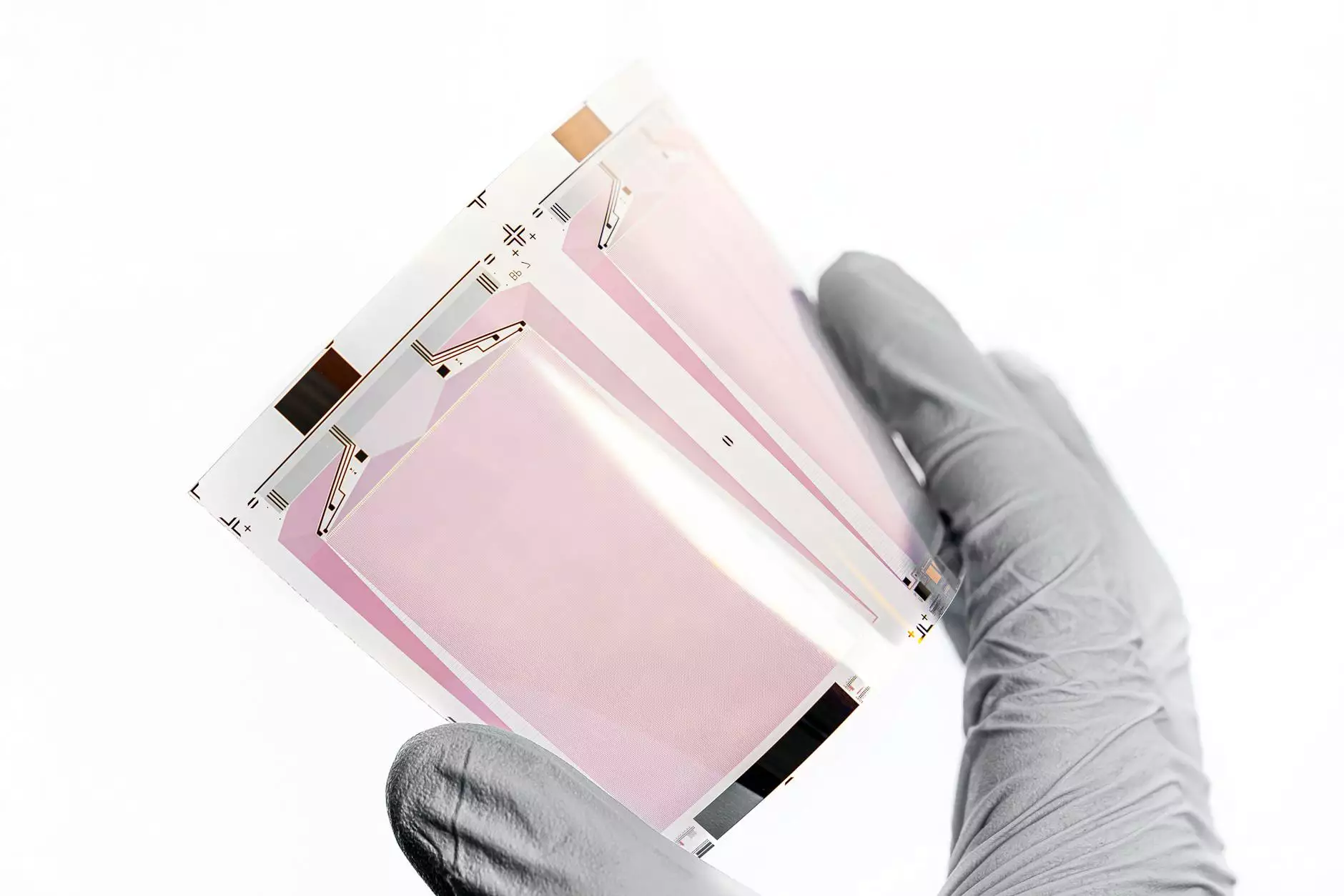
In today's fast-paced industrial world, the role of cnc precision parts manufacturers has evolved dramatically. As businesses aim to enhance their production capacities while maintaining high standards of quality, precision in manufacturing becomes paramount. This article delves into the intricate world of CNC (Computer Numerical Control) machining and its critical importance in the metal fabrication industry.
Understanding CNC Machining
CNC machining is a method used to control machine tools via a computer. This technology allows for highly precise manufacturing of parts, which is essential in sectors such as aerospace, automotive, and medical equipment. With the advent of CNC technology, manufacturers can produce intricate designs that were once deemed impossible manually.
The Evolution of CNC Precision Parts Manufacturing
Since its inception, CNC machining has undergone several advancements, leading to enhanced efficiency, precision, and flexibility. The following points illustrate how CNC technology has matured over the years:
- Increased Automation: Modern CNC machines are equipped with advanced automation features, significantly reducing labor costs and human errors.
- Enhanced Software: Sophisticated CAD (Computer-Aided Design) and CAM (Computer-Aided Manufacturing) software play a central role in designing and manufacturing parts with unmatched accuracy.
- Material Versatility: CNC machining now accommodates a wide variety of materials, including metals like aluminum, steel, and titanium, as well as plastics and composites.
- Shortened Production Time: The speed at which CNC machines operate allows manufacturers to deliver products faster, meeting tight market demands.
The Importance of Precision in Manufacturing
Precision is a cornerstone in manufacturing, particularly for industries that require tightly controlled specifications. Here’s why precision matters:
- Quality Assurance: Precision manufacturing ensures consistent quality, thereby reducing waste and the likelihood of product recalls.
- Cost Efficiency: By minimizing errors and scrap, manufacturers can significantly reduce operational costs.
- Safety Standards: In sectors like aerospace and healthcare, precision is critical to ensure safety and reliability.
- Competitive Advantage: Companies that emphasize precision in manufacturing can differentiate themselves in the marketplace.
How CNC Precision Parts Manufacturers Enhance Production
CNC precision parts manufacturers significantly boost the production capabilities of businesses through several key strategies:
1. Advanced Technology Integration
Manufacturers are continually updating their machinery with cutting-edge technology such as 5-axis machining, which allows for complex part geometries without the need for multiple setups. This capability dramatically enhances productivity and reduces lead times.
2. Customization and Flexibility
Today’s customers demand tailored solutions, and CNC manufacturers are adept at creating custom parts that meet specific needs. This is accomplished through advanced CAD/CAM systems that facilitate rapid changes and adjustments to designs.
3. Quality Control Systems
Implementing rigorous quality control protocols enables manufacturers to maintain high standards. From automated inspection systems that utilize laser scanning and vision measurement to manual checks, ensuring that every part meets the set specifications is a top priority.
The Role of CNC Precision Parts Manufacturers in Metal Fabricators
The metal fabrication sector greatly benefits from the services provided by CNC precision parts manufacturers through:
- Rapid Prototyping: CNC machining allows for quick turnaround times on prototypes, enabling engineers to test and iterate designs efficiently.
- Large-Scale Production: With high-speed CNC machines, manufacturers can produce thousands of identical parts with ease, supporting large-scale operations.
- Complex Components: CNC technology can create components with intricate designs that require high precision, which is often seen in machined fixtures or products.
Challenges Faced by CNC Precision Parts Manufacturers
Despite the benefits, CNC precision parts manufacturers encounter several challenges:
- High Initial Investment: CNC machinery and software require a significant capital investment, which can be a barrier for smaller manufacturers.
- Skilled Labor Shortage: There is an ongoing demand for skilled technicians who can operate CNC machines and program designs accurately.
- Technological Advancements: Keeping up with the pace of technological advancements and integrating new technologies into existing workflows can be challenging.
Future Trends in CNC Precision Parts Manufacturing
The future of CNC precision parts manufacturing is promising, driven by innovations and trends that redefine the industry:
1. Smart Manufacturing
The integration of IoT (Internet of Things) in manufacturing processes leads to smarter systems that can predict failures, perform real-time monitoring, and streamline operations.
2. Additive Manufacturing
Combining CNC machining with additive processes (like 3D printing) will expand manufacturing capabilities, allowing for innovative design possibilities and materials usage.
3. Sustainability Practices
As businesses increasingly prioritize environmentally friendly practices, CNC manufacturers will adopt sustainable methods, including waste reduction and energy efficiency improvements.
Conclusion: The Path Forward for CNC Precision Parts Manufacturers
In conclusion, the landscape of cnc precision parts manufacturers within the metal fabrication industry is continually evolving. By embracing technological advancements, focusing on quality, and addressing the challenges head-on, manufacturers can thrive in this competitive market. Investing in precision technology not only enhances production capabilities but also establishes a foundation for future growth and innovation.
As a leader in metal fabrication, DeepMould exemplifies the dedication and innovation that define the future of CNC precision manufacturing. Whether it’s through advanced machining techniques or a commitment to quality, DeepMould is poised to support industries with top-notch precision parts, driving prosperity in modern manufacturing.