Understanding Spiral Freezer Manufacturers and Their Role in the Food Industry
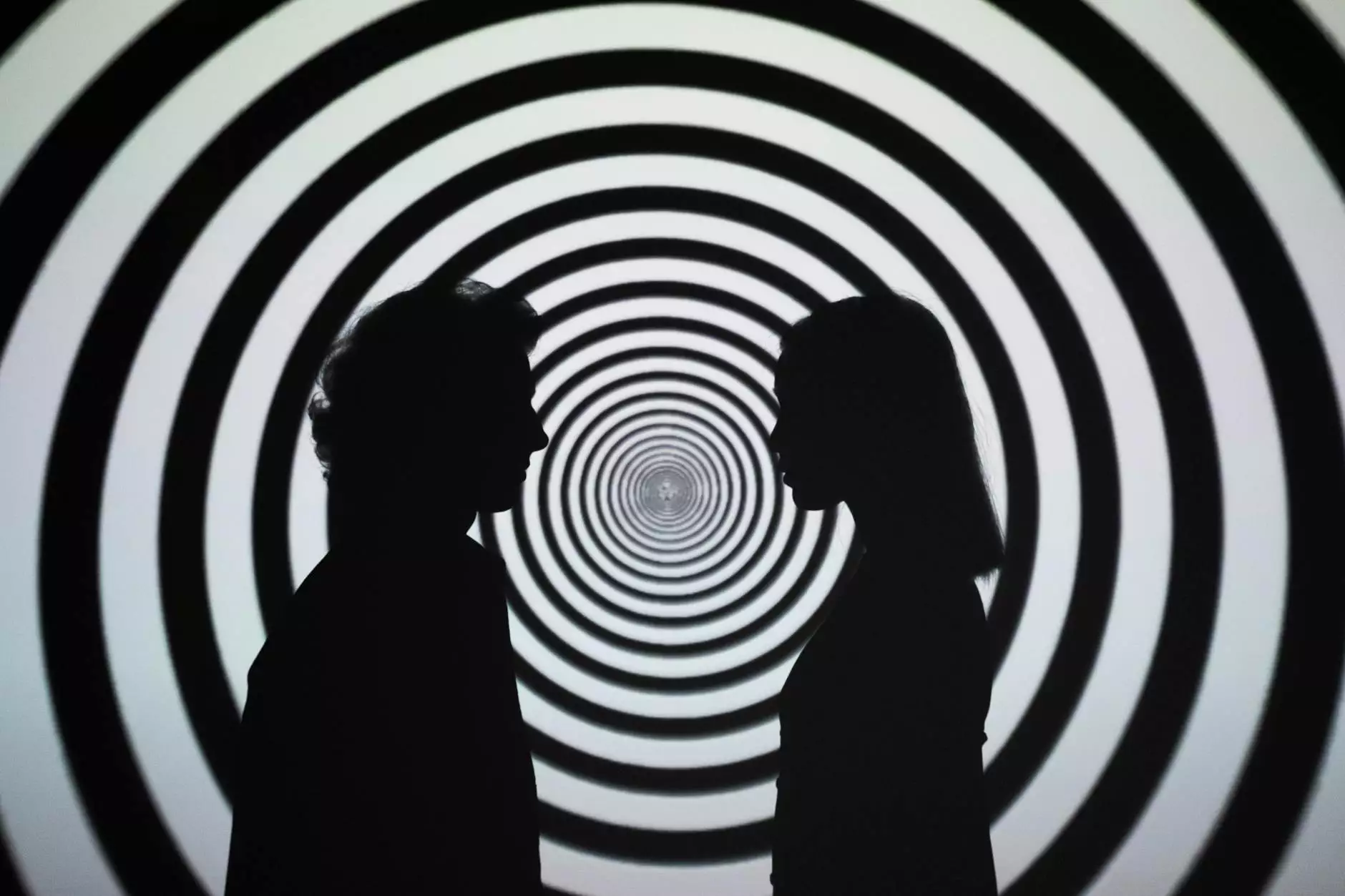
The food processing and storage industry has evolved dramatically over the past few decades, primarily due to the advancements in technology and the need for more efficient refrigeration solutions. Among these technological marvels, spiral freezers have taken center stage due to their efficiency and effectiveness. In this article, we will delve deep into the world of spiral freezer manufacturers, exploring their importance, functions, and the various aspects that make them pivotal in the refrigeration ecosystem.
What is a Spiral Freezer?
A spiral freezer is a type of industrial freezer that utilizes a unique design to freeze food products rapidly and efficiently. Unlike traditional freezers, which may have flat surfaces, spiral freezers employ a helical configuration that allows for continuous movement of products through a freezing tunnel. This design promotes better air circulation and enables uniform freezing, making it an ideal choice for numerous applications.
The Importance of Spiral Freezers in Food Processing
The significance of spiral freezers extends beyond mere temperature control; they are crucial in maintaining the quality, safety, and integrity of food products. Here are some vital roles they play:
- Rapid Freezing: Spiral freezers significantly reduce freezing times, which helps in retaining the nutritional value and texture of the food.
- Quality Preservation: These freezers prevent the formation of large ice crystals that can damage cell structures in food, ensuring the freshness of the product.
- Space Efficiency: The vertical design of spiral freezers maximizes floor space, allowing food manufacturers to optimize their production lines.
- Energy Efficiency: Advanced spiral freezing technology often results in lower energy consumption compared to traditional freezing methods.
Types of Spiral Freezers Offered by Manufacturers
Spiral freezer manufacturers produce a range of models to meet different industry needs. Here’s a closer look at the types:
1. Continuous Spiral Freezers
These are designed for high-volume production. Continuous spiral freezers allow products to move through the freezing process without interruption, making them perfect for large manufacturers dealing with bulk amounts of food.
2. Batch Spiral Freezers
Designed for smaller operations, batch spiral freezers are suitable for production that requires a variety of products. They can freeze multiple products in batches, providing flexibility for different processing needs.
3. Low-Temperature Spiral Freezers
These are specialized units designed to reach extremely low temperatures. They are ideal for freezing sensitive products like ice cream and certain meat products which require precise temperature control to maintain quality.
Key Features to Consider When Choosing a Spiral Freezer Manufacturer
When selecting a spiral freezer, it's essential to consider several factors to ensure you get the right fit for your operations:
- Capacity: Assess your production volume needs to choose a freezer with adequate capacity.
- Temperature Range: Ensure the freezer can achieve the necessary temperatures for your specific products.
- Energy Efficiency: Look for manufacturers that offer energy-efficient models to reduce operational costs.
- Customization Options: Some manufacturers provide customizable features to fit your specific requirements.
- Material Quality: Ensure that the materials used in construction can withstand industrial use and comply with food safety regulations.
The Process of Freezing in Spiral Freezers
The operation of a spiral freezer is a streamlined process that ensures products are frozen quickly and uniformly. Here’s an overview of how it works:
1. Product Loading
Food products are loaded onto an inclined conveyor belt that leads into the spiral freezing chamber. The innovative design allows for a continuous feed, maximizing the throughput.
2. Airflow Management
High-velocity fans circulate frigid air throughout the spiraled freezing path. This ensures that every product receives an equal amount of cold air, promoting uniform freezing.
3. Monitoring Temperature
Advanced spiral freezer systems come with integrated temperature probes and controllers, ensuring that the products remain at the desired freezing temperature throughout the process.
4. Product Discharge
Once the products are frozen to the required temperature, they are discharged at the bottom of the spiral freezer and ready for packaging or further processing.
Benefits of Working with Reliable Spiral Freezer Manufacturers
Partnering with established spiral freezer manufacturers offers numerous advantages that can significantly impact your business operations:
- Expertise and Support: Reputable manufacturers often provide extensive technical support and guidance during the purchasing process and beyond.
- Innovation: Leading manufacturers are continuously innovating, which means you have access to the latest technologies and efficiencies.
- Warranty and Service Plans: Reliable manufacturers usually offer warranties and service plans that can save you costs on potential repairs and maintenance.
- Compliance: Established manufacturers adhere to the highest industry standards for food safety, ensuring compliance with regulatory requirements.
Cost Considerations When Buying a Spiral Freezer
The investment in a spiral freezer can vary significantly based on several factors. Here are key considerations that affect cost:
- Size and Capacity: Larger freezers usually come at a higher price but provide greater capacity and productivity.
- Customization: Additional features such as automation, modified designs, or specialized material construction can increase costs.
- Brand Reputation: Established brands might have higher upfront costs but often provide better reliability and service.
- Energy Efficiency Ratings: Though more energy-efficient models may have higher initial costs, they often save money over time through lower operating costs.
Future Trends in Spiral Freezer Technology
As the food industry continues to evolve, spiral freezer technology is also advancing. Here are some trends that spiral freezer manufacturers are focusing on:
1. Increased Automation
With the rise of smart factories and Industry 4.0, many manufacturers are integrating automation into their freezing systems, significantly improving efficiency and reducing labor costs.
2. Sustainability Measures
Environmental considerations are leading manufacturers to design freezers that use refrigerants with lower global warming potentials and implement energy-efficient designs.
3. Advanced Monitoring Systems
Real-time monitoring technologies enable manufacturers to track the freezing process remotely, reducing chances of errors and enhancing operational efficiency.
Conclusion
In summary, spiral freezer manufacturers are pivotal players in the refrigeration equipment sector, providing essential solutions that meet the demands of food processing and preservation. By understanding the technology, benefits, and factors surrounding spiral freezers, businesses can make informed purchasing decisions, optimizing their operations for efficiency and quality. As the industry continues to innovate, staying abreast of the latest trends in freezer technology will be vital for maintaining a competitive edge.
Whether you are involved in small-scale production or large manufacturing setups, investing in a high-quality spiral freezer from a reputable manufacturer can significantly enhance your outputs while ensuring product integrity. Always consider consulting with experienced professionals within the field to make the best-informed choice for your business needs.